Knowledge and Selection of Temperature Sensors
(1) Basic concepts of temperature measurement
1. Temperature definition:
Temperature is a physical quantity that represents the degree of hotness or coldness of an object. Temperature can only be measured indirectly through certain characteristics of an object that change with temperature, and the scale used to measure the temperature value of an object is called a temperature scale. It specifies the starting point for temperature readings (zero point) and the basic unit for measuring temperature. Currently, the most commonly used temperature scales in the world include the Fahrenheit temperature scale, the Celsius temperature scale, the thermodynamic temperature scale and the International Practical Temperature Scale.
The Celsius temperature scale (℃) stipulates that under standard atmospheric pressure, the melting point of ice is 0 degrees and the boiling point of water is 100 degrees. Divide it into 100 equal parts in the middle, each divided into 1 degree Celsius, and the symbol is ℃.
The Fahrenheit temperature scale (℉) stipulates that at standard atmospheric pressure, the melting point of ice is 32 degrees and the boiling point of water is 212 degrees. Divide 180 equal parts in the middle, each equal part is 1 degree Fahrenheit and the symbol is ℉.
The thermodynamic temperature scale (symbol T) is also called the Kelvin temperature scale (symbol K), or the absolute temperature scale, which stipulates that the temperature when molecular motion stops is absolute zero.
International Temperature Scale: The International Practical Temperature Scale is an internationally agreed temperature scale that is close to the thermodynamic temperature scale, has high reproduction accuracy and is easy to use. The current internationally accepted temperature scale is the "1968 International Practical Temperature Scale - 1975 Revised Edition" adopted by the 15th International Conference on Temperature in 1975, recorded as: IPTS-68 (REV-75). However, due to certain inaccuracies in the IPTS-68 temperature, the International Committee for Weights and Measures authorized the 1989 meeting to adopt the 1990 International ITS-90 in Resolution No. 7 of the 18th International Conference on Weights and Measures. ITS-90 temperature scale replaces IPS-68. my country has fully implemented the ITS-90 international temperature scale since January 1, 1994.
1990 International Temperature Scale:
a. Temperature unit: Thermodynamic temperature is a basic physical quantity. Its unit is Kelvin, which is defined as 1/273.16 of the thermodynamic temperature of the triple point of water. The difference from 273.15K (freezing point) is used to express temperature, so this method is still retained. By definition, the magnitude of Celsius is equal to Kelvin, and temperature differences can also be expressed in degrees Celsius or Kelvin. The International Temperature Scale ITS-90 defines both the international temperature in Kelvin (symbol T90) and the international temperature in Celsius (symbol t90).
b. General principles of the International Temperature Scale ITS-90: ITS-90 ranges from 0.65K upward to the highest temperature that can actually be measured using monochromatic radiation according to Planck's radiation law. ITS-90 is formulated in such a way that it is the best estimate of T at any temperature over the full range. Compared with direct measurement of thermodynamic temperature, T90 measurement is much more convenient, more precise, and has high reproducibility.
c. Definition of ITS-90:
The first temperature zone is between 0.65K and 5.00K. T90 is defined by the relationship between the vapor pressure and temperature of 3He and 4He.
The second temperature zone is defined by the helium gas thermometer between 3.0K and the triple point of neon (24.5661K).
The third temperature zone is between the triple point of hydrogen (13.8033K) and the freezing point of silver (961.78℃). T90 is defined by a platinum resistance thermometer. It is scaled using a prescribed set of defined interpolations. In the temperature zone above the freezing point of silver (961.78°C), T90 is defined according to Planck's radiation law, and the reproduction instrument is an optical pyrometer.
(2.) Classification of temperature measuring instruments
Temperature measuring instruments can be divided into two categories: contact type and non-contact type according to the temperature measurement method. Generally speaking, contact temperature measuring instruments are relatively simple, reliable, and have high measurement accuracy. However, since the temperature measuring element and the medium to be measured require sufficient thermal communication, it takes a certain amount of time to reach thermal equilibrium, so there is a delay in temperature measurement, and it is also limited by high temperature resistant materials. It cannot be used for very high temperature measurements. Non-contact instrument temperature measurement measures temperature through the principle of thermal radiation. The measuring element does not need to be in contact with the measured medium, has a wide temperature measurement range, is not restricted by the upper limit of temperature measurement, and will not destroy the temperature field of the measured object. The reaction speed is generally faster. However, due to the influence of external factors such as the emissivity of the object, measurement distance, smoke, dust and water vapor, the measurement error is large.
(3.) Selection of sensors
The national standard GB7665-87 defines a sensor as: "a device or device that can sense the specified measured value and convert it into a usable signal according to certain rules. It is usually composed of a sensitive element and a conversion element." A sensor is a detection device that can sense the measured information and convert the sensed information into electrical signals or other required forms of information output according to certain rules. To meet the requirements of information transmission, processing, storage, display, recording and control. It is the primary link to realize automatic detection and automatic control.
(1) Modern sensors vary widely in principle and structure. How to reasonably select sensors according to the specific measurement purpose, measurement object and measurement environment is the first problem to be solved when measuring a certain quantity. After the sensor is determined, the matching measurement methods and measurement equipment can also be determined. The success or failure of the measurement results depends to a large extent on whether the sensor selection is reasonable.
1. Determine the type of sensor based on the measurement object and measurement environment: To carry out a specific measurement work, you must first consider what principle the sensor uses, which can only be determined after analyzing many factors. Because, even if the same physical quantity is measured, there are sensors with multiple principles to choose from. Which principle of sensor is more suitable? You need to consider the following specific issues based on the characteristics of the measured object and the use conditions of the sensor: the size of the measuring range; the volume requirements of the sensor at the measured location. The measurement method is contact or non-contact; the signal extraction method is wired or non-contact measurement; the source of the sensor is imported or domestic, and whether the price is acceptable or self-developed.
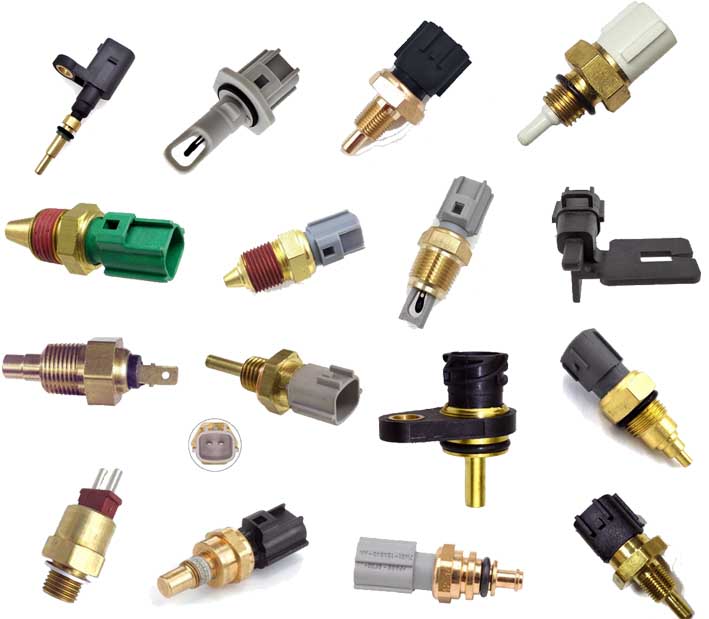
2. Selection of sensitivity: Generally, within the linear range of the sensor, it is hoped that the higher the sensitivity of the sensor, the better, because only when the sensitivity is high, the output signal corresponding to the measured change will be relatively large, which is conducive to signal processing. However, it should be noted that the sensor has high sensitivity, and external noise unrelated to the measurement is easily mixed in, and will be amplified by the amplification system, affecting the measurement accuracy. Therefore, the sensor itself is required to have a high signal-to-noise ratio to minimize factory-worry signals introduced from the outside world. The sensitivity of the sensor is directional. When the measured vector is a single vector and its directivity requirements are high, sensors with smaller sensitivity in other directions should be selected. If the measured value is a multi-dimensional vector, the cross-sensitivity of the sensor must be as small as possible.
3. Frequency response characteristics: The frequency response characteristics of the sensor determine the frequency range to be measured, and measurement conditions without distortion must be maintained within the allowed frequency range. In fact, there is always a certain delay in the sensor's response, and we hope that the delay will be as short as possible. The frequency response of the sensor is high, and the measurable signal frequency range is wide. Due to the influence of structural characteristics, the inertia of the mechanical system is large, and the measurable signal frequency of the low-frequency sensor is low. In dynamic measurement, the response characteristics should be based on the characteristics of the signal (steady state, random, etc.) to avoid excessive errors.
4. Linear range: The linear range of the sensor refers to the range in which the output is proportional to the input. Theoretically, within this range, the sensitivity remains constant. The wider the linear range of the sensor, the larger its measuring range and a certain measurement accuracy can be guaranteed. When selecting a sensor, after the sensor type is determined, you must first check whether its measuring range meets the requirements. But in fact, no sensor can guarantee absolute linearity, and its linearity is also relative. When the required measurement accuracy is relatively low, a sensor with a small nonlinear error can be approximately regarded as linear within a certain range, which will bring great convenience to the measurement.
5. Stability: The ability of a sensor to maintain its performance unchanged after being used for a period of time is called stability. In addition to the structure of the sensor itself, the factors that affect the long-term stability of the sensor are mainly the environment in which the sensor is used. Therefore, in order for the sensor to have good stability, the sensor must have strong environmental adaptability. Before selecting a sensor, its usage environment should be investigated, and appropriate sensors should be selected according to the specific usage environment, or appropriate measures should be taken to reduce environmental impact. In some situations where the sensor is required to be used for a long time and can be easily replaced or calibrated, the stability requirements of the selected sensor are more stringent and must be able to withstand the test of a long time.
6. Accuracy: Accuracy is an important performance indicator of the sensor. It is an important link related to the measurement accuracy of the entire measurement system. The higher the accuracy of the sensor, the more expensive it is. Therefore, the accuracy of the sensor only needs to meet the accuracy requirements of the entire measurement system, and there is no need to select it too high. This makes it possible to choose a cheaper and simpler sensor among many that satisfy the same measurement. If the purpose of measurement is qualitative analysis, it is enough to choose a sensor with high repeatability accuracy. It is not suitable to choose a sensor with high absolute value accuracy. If it is for quantitative analysis and it is necessary to obtain accurate measurement values, it is necessary to select a sensor with an accuracy level that meets the requirements. For some special use occasions, if a suitable sensor cannot be selected, the sensor must be designed and manufactured by oneself. The performance of the self-made sensor should meet the usage requirements.
(2) Thermometer:
1. Thermal resistance: The thermal resistance is the most commonly used temperature detector in medium and low temperature areas. Its main features are high measurement accuracy and stable performance. Among them, the measurement accuracy of platinum thermal resistance is the highest. It is not widely used in industrial temperature measurement and is made into a standard reference instrument.
① Thermal resistance temperature measurement principle and materials: Thermal resistance temperature measurement is based on the characteristic that the resistance value of a metal conductor increases with the increase of temperature to measure temperature. Thermal resistors are mostly made of metal materials. The most commonly used ones are platinum and copper. In addition, rhodium, nickel, manganese and other materials have been used to make thermal resistors.
② Composition of the thermal resistance temperature measurement system: The thermal resistance temperature measurement system generally consists of a thermal resistor, connecting wires and a digital temperature control display meter. Two points must be noted: "The graduation numbers of the thermal resistor and the digital temperature control display meter must be consistent; in order to eliminate the influence of changes in resistance of the connecting wires, a three-wire connection method must be adopted."
2. Thermistor: NTC thermistor has the characteristics of small size, high testing accuracy, fast response speed, stability and reliability, anti-aging, interchangeability, and good consistency. Widely used in air conditioning, heating equipment, electronic thermometers, liquid level sensors, automotive electronics, electronic desk calendars and other fields.
3. Thermocouple: Thermocouple is one of the most commonly used temperature detection components in industry. The advantages are:
① High measurement accuracy. Because the thermocouple is in direct contact with the object being measured, it is not affected by the intermediate medium.
②Wide measuring range. Commonly used thermocouples can continuously measure from -50 to +1600°C. Some special thermocouples have a minimum temperature of -269℃ (such as gold, iron, nickel and chromium) and a maximum temperature of +2800℃ (such as tungsten-rhenium).
③ Simple structure and easy to use. Thermocouples are usually composed of two different metal wires and are not limited by size or opening. There is a protective sleeve outside, which is very convenient to use.
(1). Basic principles of thermocouple temperature measurement
Welding two conductors or semiconductors A and B of different materials together to form a closed circuit. When there is a temperature difference between the two attachment points 1 and 2 of conductors A and B, an electromotive force is generated between the two, thus forming a large current in the loop. This phenomenon is called the thermoelectric effect. Thermocouples take advantage of this effect to work.
(2). Types of thermocouples
Commonly used thermocouples can be divided into two categories: standard thermocouples and non-standard thermocouples.
Standard thermocouples refer to thermocouples whose national standards stipulate the relationship between thermoelectric potential and temperature, allowable errors, and have a unified standard scale. It has matching display instruments for selection.
Non-standardized thermocouples are inferior to standardized thermocouples in terms of use range or magnitude. Generally, there is no unified graduation table, and they are mainly used for measurements in certain special occasions.
Since January 1, 1988, in my country, all thermocouples and thermal resistors have been produced in accordance with IEC international standards. And designated seven types of standardized thermocouples, S, B, E, K, R, J, and T, as my country's unified design thermocouples.
(3). Temperature Compensation of Thermocouple Cold Junction
Since the materials of thermocouples are generally relatively expensive (especially when precious metals are used), the distance between the temperature measurement point and the instrument is very long. In order to save thermocouple materials and reduce costs, compensation wires are usually used to extend the cold end (free end) of the thermocouple to the control room where the temperature is relatively stable, and connect it to the instrument terminals. It must be noted that the function of the thermocouple compensation wire is only to extend the hot electrode so that the cold end of the thermocouple moves to the instrument terminals in the control room. It itself cannot eliminate the influence of cold end temperature changes on temperature measurement and does not have a compensation effect. Therefore, other correction methods need to be used to compensate for the impact on temperature measurement when the cold end temperature t0≠0℃. When using the thermocouple compensation wire, you must pay attention to the matching model, the polarity cannot be wrong, and the temperature of the compensation wire and the thermocouple connection end cannot exceed 100°C.
4. my country’s eight major developments in the field of temperature control
my country's instrumentation has kept pace with international development in terms of miniaturization, digitization, intelligence, integration and networking, and has made significant progress in the development, research and industrialization of parts with independent intellectual property rights. Among them, the major scientific and technological progress worth mentioning mainly include the following eight aspects:
1. Advanced industrial automation instruments and systems have achieved modularization and full digital integration, meeting industrialization requirements. It is widely used in steel, electricity, coal, chemicals, oil, transportation, construction, national defense, food, medicine, agriculture, environmental protection and other fields, taking a solid step towards having independent intellectual property rights.
2. The research and industrialization level of intelligent series test instruments and automatic test systems have been greatly improved. It has established automatic testing systems for various industries such as aerospace testing, electromechanical product testing, household appliance testing, earthquake monitoring, meteorological detection, and environmental monitoring. The overall level reaches
to the level of advanced foreign products, but the price is significantly lower than foreign products.
3. The successful development and mass production of microwave and millimeter wave vector network analyzers marks that my country has become the second country in the world after the United States to produce such high-precision instruments.
4. Research and develop nanometer measurement and control and micro-instruments with its own characteristics. It is a world leader in the directional preparation of carbon nanotubes and the detection of structure and physical properties.
5. Complete the complete electrical quantum standard and the 1.5×10-5 national electrical energy standard device, making my country’s electrical measurement standards at the internationally advanced level.
6. Carry out research on scientific instruments with independent intellectual property rights and improve the overall level of scientific instruments in our country.
7. Established a development mechanism that combines industry, academia and research, and domestic and foreign cooperation, and expanded the application fields of scientific instruments, such as the successful development of spectroscopic instruments for customs anti-counterfeiting documents. After being promoted by customs across the country, a total of 54 billion yuan worth of counterfeit tickets have been seized, saving the country huge economic losses. The market share of domestic scientific instruments increased from 13% during the Eighth Five-Year Plan to 25% at the end of the Ninth Five-Year Plan.
8. The high-intensity focused ultrasound tumor treatment system was successfully developed and mass-produced. Ultrasound medical instruments have international leading advantages in non-invasive tumor treatment.
1. Temperature definition:
Temperature is a physical quantity that represents the degree of hotness or coldness of an object. Temperature can only be measured indirectly through certain characteristics of an object that change with temperature, and the scale used to measure the temperature value of an object is called a temperature scale. It specifies the starting point for temperature readings (zero point) and the basic unit for measuring temperature. Currently, the most commonly used temperature scales in the world include the Fahrenheit temperature scale, the Celsius temperature scale, the thermodynamic temperature scale and the International Practical Temperature Scale.
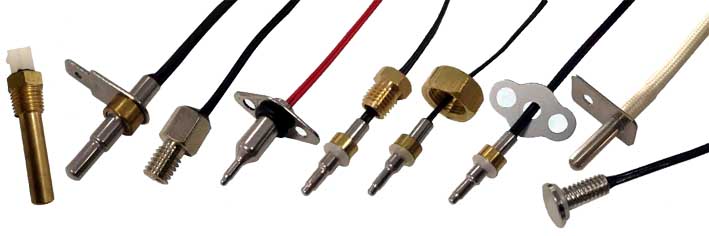
The Fahrenheit temperature scale (℉) stipulates that at standard atmospheric pressure, the melting point of ice is 32 degrees and the boiling point of water is 212 degrees. Divide 180 equal parts in the middle, each equal part is 1 degree Fahrenheit and the symbol is ℉.
The thermodynamic temperature scale (symbol T) is also called the Kelvin temperature scale (symbol K), or the absolute temperature scale, which stipulates that the temperature when molecular motion stops is absolute zero.
International Temperature Scale: The International Practical Temperature Scale is an internationally agreed temperature scale that is close to the thermodynamic temperature scale, has high reproduction accuracy and is easy to use. The current internationally accepted temperature scale is the "1968 International Practical Temperature Scale - 1975 Revised Edition" adopted by the 15th International Conference on Temperature in 1975, recorded as: IPTS-68 (REV-75). However, due to certain inaccuracies in the IPTS-68 temperature, the International Committee for Weights and Measures authorized the 1989 meeting to adopt the 1990 International ITS-90 in Resolution No. 7 of the 18th International Conference on Weights and Measures. ITS-90 temperature scale replaces IPS-68. my country has fully implemented the ITS-90 international temperature scale since January 1, 1994.
1990 International Temperature Scale:
a. Temperature unit: Thermodynamic temperature is a basic physical quantity. Its unit is Kelvin, which is defined as 1/273.16 of the thermodynamic temperature of the triple point of water. The difference from 273.15K (freezing point) is used to express temperature, so this method is still retained. By definition, the magnitude of Celsius is equal to Kelvin, and temperature differences can also be expressed in degrees Celsius or Kelvin. The International Temperature Scale ITS-90 defines both the international temperature in Kelvin (symbol T90) and the international temperature in Celsius (symbol t90).
b. General principles of the International Temperature Scale ITS-90: ITS-90 ranges from 0.65K upward to the highest temperature that can actually be measured using monochromatic radiation according to Planck's radiation law. ITS-90 is formulated in such a way that it is the best estimate of T at any temperature over the full range. Compared with direct measurement of thermodynamic temperature, T90 measurement is much more convenient, more precise, and has high reproducibility.
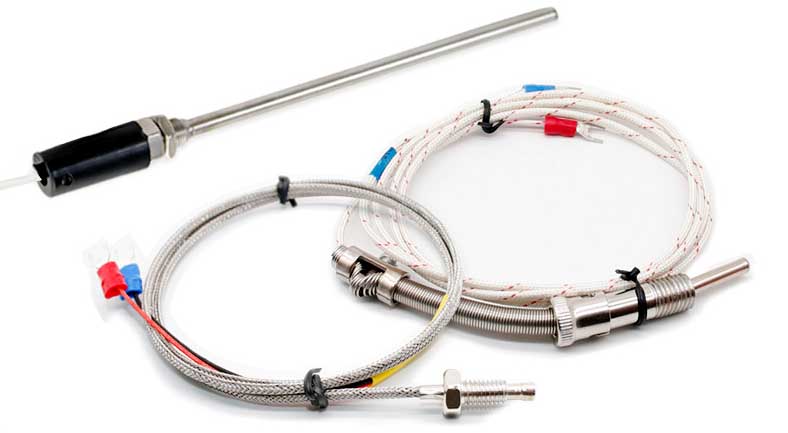
The first temperature zone is between 0.65K and 5.00K. T90 is defined by the relationship between the vapor pressure and temperature of 3He and 4He.
The second temperature zone is defined by the helium gas thermometer between 3.0K and the triple point of neon (24.5661K).
The third temperature zone is between the triple point of hydrogen (13.8033K) and the freezing point of silver (961.78℃). T90 is defined by a platinum resistance thermometer. It is scaled using a prescribed set of defined interpolations. In the temperature zone above the freezing point of silver (961.78°C), T90 is defined according to Planck's radiation law, and the reproduction instrument is an optical pyrometer.
(2.) Classification of temperature measuring instruments
Temperature measuring instruments can be divided into two categories: contact type and non-contact type according to the temperature measurement method. Generally speaking, contact temperature measuring instruments are relatively simple, reliable, and have high measurement accuracy. However, since the temperature measuring element and the medium to be measured require sufficient thermal communication, it takes a certain amount of time to reach thermal equilibrium, so there is a delay in temperature measurement, and it is also limited by high temperature resistant materials. It cannot be used for very high temperature measurements. Non-contact instrument temperature measurement measures temperature through the principle of thermal radiation. The measuring element does not need to be in contact with the measured medium, has a wide temperature measurement range, is not restricted by the upper limit of temperature measurement, and will not destroy the temperature field of the measured object. The reaction speed is generally faster. However, due to the influence of external factors such as the emissivity of the object, measurement distance, smoke, dust and water vapor, the measurement error is large.
(3.) Selection of sensors
The national standard GB7665-87 defines a sensor as: "a device or device that can sense the specified measured value and convert it into a usable signal according to certain rules. It is usually composed of a sensitive element and a conversion element." A sensor is a detection device that can sense the measured information and convert the sensed information into electrical signals or other required forms of information output according to certain rules. To meet the requirements of information transmission, processing, storage, display, recording and control. It is the primary link to realize automatic detection and automatic control.
(1) Modern sensors vary widely in principle and structure. How to reasonably select sensors according to the specific measurement purpose, measurement object and measurement environment is the first problem to be solved when measuring a certain quantity. After the sensor is determined, the matching measurement methods and measurement equipment can also be determined. The success or failure of the measurement results depends to a large extent on whether the sensor selection is reasonable.
1. Determine the type of sensor based on the measurement object and measurement environment: To carry out a specific measurement work, you must first consider what principle the sensor uses, which can only be determined after analyzing many factors. Because, even if the same physical quantity is measured, there are sensors with multiple principles to choose from. Which principle of sensor is more suitable? You need to consider the following specific issues based on the characteristics of the measured object and the use conditions of the sensor: the size of the measuring range; the volume requirements of the sensor at the measured location. The measurement method is contact or non-contact; the signal extraction method is wired or non-contact measurement; the source of the sensor is imported or domestic, and whether the price is acceptable or self-developed.
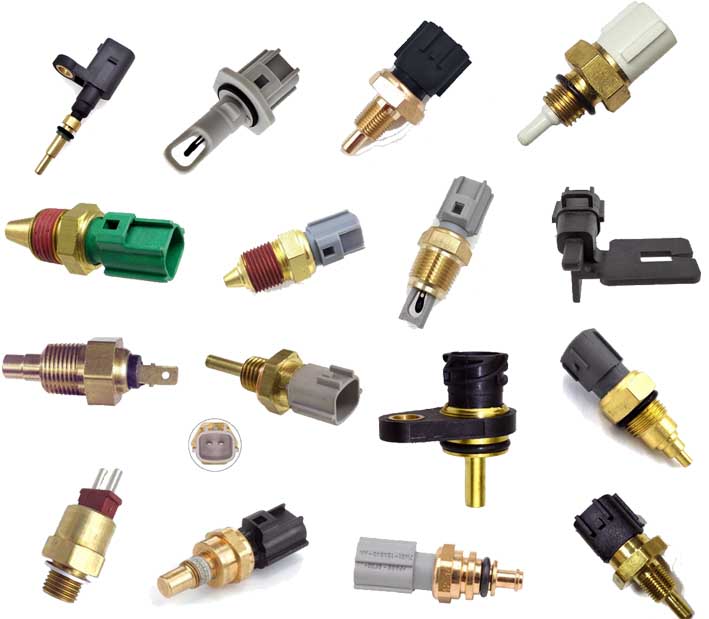
2. Selection of sensitivity: Generally, within the linear range of the sensor, it is hoped that the higher the sensitivity of the sensor, the better, because only when the sensitivity is high, the output signal corresponding to the measured change will be relatively large, which is conducive to signal processing. However, it should be noted that the sensor has high sensitivity, and external noise unrelated to the measurement is easily mixed in, and will be amplified by the amplification system, affecting the measurement accuracy. Therefore, the sensor itself is required to have a high signal-to-noise ratio to minimize factory-worry signals introduced from the outside world. The sensitivity of the sensor is directional. When the measured vector is a single vector and its directivity requirements are high, sensors with smaller sensitivity in other directions should be selected. If the measured value is a multi-dimensional vector, the cross-sensitivity of the sensor must be as small as possible.
3. Frequency response characteristics: The frequency response characteristics of the sensor determine the frequency range to be measured, and measurement conditions without distortion must be maintained within the allowed frequency range. In fact, there is always a certain delay in the sensor's response, and we hope that the delay will be as short as possible. The frequency response of the sensor is high, and the measurable signal frequency range is wide. Due to the influence of structural characteristics, the inertia of the mechanical system is large, and the measurable signal frequency of the low-frequency sensor is low. In dynamic measurement, the response characteristics should be based on the characteristics of the signal (steady state, random, etc.) to avoid excessive errors.
4. Linear range: The linear range of the sensor refers to the range in which the output is proportional to the input. Theoretically, within this range, the sensitivity remains constant. The wider the linear range of the sensor, the larger its measuring range and a certain measurement accuracy can be guaranteed. When selecting a sensor, after the sensor type is determined, you must first check whether its measuring range meets the requirements. But in fact, no sensor can guarantee absolute linearity, and its linearity is also relative. When the required measurement accuracy is relatively low, a sensor with a small nonlinear error can be approximately regarded as linear within a certain range, which will bring great convenience to the measurement.
5. Stability: The ability of a sensor to maintain its performance unchanged after being used for a period of time is called stability. In addition to the structure of the sensor itself, the factors that affect the long-term stability of the sensor are mainly the environment in which the sensor is used. Therefore, in order for the sensor to have good stability, the sensor must have strong environmental adaptability. Before selecting a sensor, its usage environment should be investigated, and appropriate sensors should be selected according to the specific usage environment, or appropriate measures should be taken to reduce environmental impact. In some situations where the sensor is required to be used for a long time and can be easily replaced or calibrated, the stability requirements of the selected sensor are more stringent and must be able to withstand the test of a long time.
6. Accuracy: Accuracy is an important performance indicator of the sensor. It is an important link related to the measurement accuracy of the entire measurement system. The higher the accuracy of the sensor, the more expensive it is. Therefore, the accuracy of the sensor only needs to meet the accuracy requirements of the entire measurement system, and there is no need to select it too high. This makes it possible to choose a cheaper and simpler sensor among many that satisfy the same measurement. If the purpose of measurement is qualitative analysis, it is enough to choose a sensor with high repeatability accuracy. It is not suitable to choose a sensor with high absolute value accuracy. If it is for quantitative analysis and it is necessary to obtain accurate measurement values, it is necessary to select a sensor with an accuracy level that meets the requirements. For some special use occasions, if a suitable sensor cannot be selected, the sensor must be designed and manufactured by oneself. The performance of the self-made sensor should meet the usage requirements.
(2) Thermometer:
1. Thermal resistance: The thermal resistance is the most commonly used temperature detector in medium and low temperature areas. Its main features are high measurement accuracy and stable performance. Among them, the measurement accuracy of platinum thermal resistance is the highest. It is not widely used in industrial temperature measurement and is made into a standard reference instrument.
① Thermal resistance temperature measurement principle and materials: Thermal resistance temperature measurement is based on the characteristic that the resistance value of a metal conductor increases with the increase of temperature to measure temperature. Thermal resistors are mostly made of metal materials. The most commonly used ones are platinum and copper. In addition, rhodium, nickel, manganese and other materials have been used to make thermal resistors.
② Composition of the thermal resistance temperature measurement system: The thermal resistance temperature measurement system generally consists of a thermal resistor, connecting wires and a digital temperature control display meter. Two points must be noted: "The graduation numbers of the thermal resistor and the digital temperature control display meter must be consistent; in order to eliminate the influence of changes in resistance of the connecting wires, a three-wire connection method must be adopted."
2. Thermistor: NTC thermistor has the characteristics of small size, high testing accuracy, fast response speed, stability and reliability, anti-aging, interchangeability, and good consistency. Widely used in air conditioning, heating equipment, electronic thermometers, liquid level sensors, automotive electronics, electronic desk calendars and other fields.
3. Thermocouple: Thermocouple is one of the most commonly used temperature detection components in industry. The advantages are:
① High measurement accuracy. Because the thermocouple is in direct contact with the object being measured, it is not affected by the intermediate medium.
②Wide measuring range. Commonly used thermocouples can continuously measure from -50 to +1600°C. Some special thermocouples have a minimum temperature of -269℃ (such as gold, iron, nickel and chromium) and a maximum temperature of +2800℃ (such as tungsten-rhenium).
③ Simple structure and easy to use. Thermocouples are usually composed of two different metal wires and are not limited by size or opening. There is a protective sleeve outside, which is very convenient to use.
(1). Basic principles of thermocouple temperature measurement
Welding two conductors or semiconductors A and B of different materials together to form a closed circuit. When there is a temperature difference between the two attachment points 1 and 2 of conductors A and B, an electromotive force is generated between the two, thus forming a large current in the loop. This phenomenon is called the thermoelectric effect. Thermocouples take advantage of this effect to work.
(2). Types of thermocouples
Commonly used thermocouples can be divided into two categories: standard thermocouples and non-standard thermocouples.
Standard thermocouples refer to thermocouples whose national standards stipulate the relationship between thermoelectric potential and temperature, allowable errors, and have a unified standard scale. It has matching display instruments for selection.
Non-standardized thermocouples are inferior to standardized thermocouples in terms of use range or magnitude. Generally, there is no unified graduation table, and they are mainly used for measurements in certain special occasions.
Since January 1, 1988, in my country, all thermocouples and thermal resistors have been produced in accordance with IEC international standards. And designated seven types of standardized thermocouples, S, B, E, K, R, J, and T, as my country's unified design thermocouples.
(3). Temperature Compensation of Thermocouple Cold Junction
Since the materials of thermocouples are generally relatively expensive (especially when precious metals are used), the distance between the temperature measurement point and the instrument is very long. In order to save thermocouple materials and reduce costs, compensation wires are usually used to extend the cold end (free end) of the thermocouple to the control room where the temperature is relatively stable, and connect it to the instrument terminals. It must be noted that the function of the thermocouple compensation wire is only to extend the hot electrode so that the cold end of the thermocouple moves to the instrument terminals in the control room. It itself cannot eliminate the influence of cold end temperature changes on temperature measurement and does not have a compensation effect. Therefore, other correction methods need to be used to compensate for the impact on temperature measurement when the cold end temperature t0≠0℃. When using the thermocouple compensation wire, you must pay attention to the matching model, the polarity cannot be wrong, and the temperature of the compensation wire and the thermocouple connection end cannot exceed 100°C.
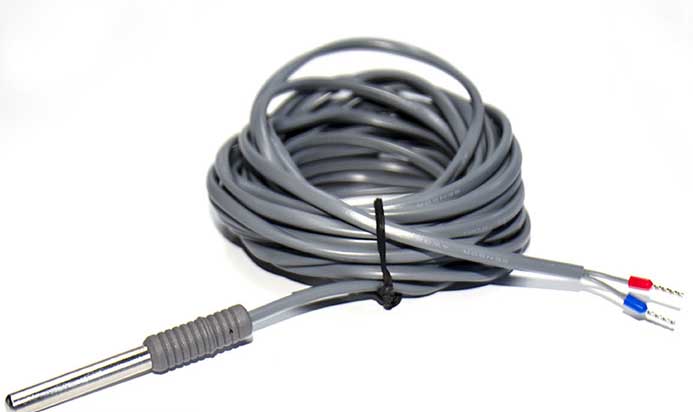
my country's instrumentation has kept pace with international development in terms of miniaturization, digitization, intelligence, integration and networking, and has made significant progress in the development, research and industrialization of parts with independent intellectual property rights. Among them, the major scientific and technological progress worth mentioning mainly include the following eight aspects:
1. Advanced industrial automation instruments and systems have achieved modularization and full digital integration, meeting industrialization requirements. It is widely used in steel, electricity, coal, chemicals, oil, transportation, construction, national defense, food, medicine, agriculture, environmental protection and other fields, taking a solid step towards having independent intellectual property rights.
2. The research and industrialization level of intelligent series test instruments and automatic test systems have been greatly improved. It has established automatic testing systems for various industries such as aerospace testing, electromechanical product testing, household appliance testing, earthquake monitoring, meteorological detection, and environmental monitoring. The overall level reaches
to the level of advanced foreign products, but the price is significantly lower than foreign products.
3. The successful development and mass production of microwave and millimeter wave vector network analyzers marks that my country has become the second country in the world after the United States to produce such high-precision instruments.
4. Research and develop nanometer measurement and control and micro-instruments with its own characteristics. It is a world leader in the directional preparation of carbon nanotubes and the detection of structure and physical properties.
5. Complete the complete electrical quantum standard and the 1.5×10-5 national electrical energy standard device, making my country’s electrical measurement standards at the internationally advanced level.
6. Carry out research on scientific instruments with independent intellectual property rights and improve the overall level of scientific instruments in our country.
7. Established a development mechanism that combines industry, academia and research, and domestic and foreign cooperation, and expanded the application fields of scientific instruments, such as the successful development of spectroscopic instruments for customs anti-counterfeiting documents. After being promoted by customs across the country, a total of 54 billion yuan worth of counterfeit tickets have been seized, saving the country huge economic losses. The market share of domestic scientific instruments increased from 13% during the Eighth Five-Year Plan to 25% at the end of the Ninth Five-Year Plan.
8. The high-intensity focused ultrasound tumor treatment system was successfully developed and mass-produced. Ultrasound medical instruments have international leading advantages in non-invasive tumor treatment.