How Various Temperature Sensors Work
Temperature sensor (temperature transducer) refers to a sensor that can sense temperature and convert it into a usable output signal. Temperature sensors are the core part of temperature measurement instruments and come in many varieties. After entering the 21st century, temperature sensors are moving towards high precision, multi-function, bus standardization, high reliability and safety. High-tech directions such as developing virtual temperature sensors and network sensors, and developing single-chip temperature measurement systems are developing rapidly. The bus technology of the temperature sensor has also been standardized and can be used as a slave to communicate with the host through a dedicated bus interface. According to the measurement method, it can be divided into two categories: contact type and non-contact type. According to the characteristics of sensor materials and electronic components, they are divided into two categories: thermal resistors and thermocouples.
How the temperature sensor works
There are four main types of temperature sensors: thermocouples, thermistors, resistance temperature detectors (RTDs), and IC temperature sensors. IC temperature sensors include two types: analog output and digital output.
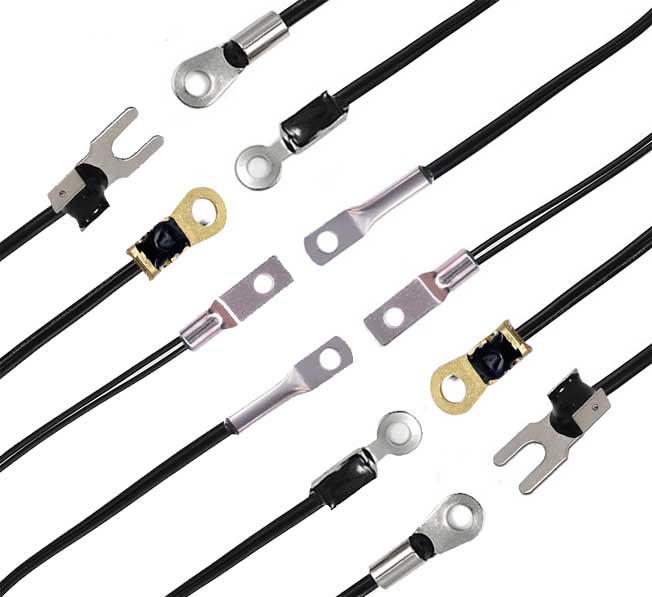
1. Working principle of thermocouple
When there are two different conductors and semiconductors A and B forming a loop, and the two ends are connected to each other, as long as the temperatures at the two nodes are different, the temperature at one end is T, which is called the working end or hot end. The temperature of the other end is TO, which is called the free end (also called the reference end) or the cold end. Then there will be current in the loop, that is, the electromotive force existing in the loop is called thermal electromotive force. This phenomenon of electromotive force generated due to temperature differences is called the Seebeck effect. There are two effects related to Seebeck: First, when a current flows through the connection of two different conductors, heat is absorbed or released (depending on the direction of the current), which is called the Peltier effect. Second, when a current flows through a conductor with a temperature gradient, the conductor absorbs or releases heat (depending on the direction of the current relative to the temperature gradient), which is called the Thomson effect. A combination of two different conductors or semiconductors is called a thermocouple. The thermoelectric potential EAB (T, T0) of the thermocouple is synthesized from the contact potential and the temperature difference potential. Contact potential refers to the potential generated at the contact between two different conductors or semiconductors. This potential is related to the properties of the two conductors or semiconductors and the temperature at the point of contact.
Thermoelectric potential refers to the potential generated by the same conductor or semiconductor at two ends with different temperatures. This potential is only related to the properties of the conductor or semiconductor and the temperature at both ends, but has nothing to do with the length, cross-sectional size of the conductor, or the temperature distribution along its length. Both contact potential and thermoelectric potential are potentials generated due to the difference in the number of electrons concentrated at the end points of the contact. The thermoelectric potential measured by a thermocouple is the composite of the two. When the loop is disconnected, there is an electromotive force difference ΔV between the disconnection points a and b, and its polarity and size are consistent with the thermoelectric potential in the loop. And it is stipulated that at the cold end, when the current flows from A to B, A is called the positive electrode and B is the negative electrode. Experiments show that when △V is very small, △V is directly proportional to △T. The differential thermoelectric potential of △V versus △T is defined as the thermoelectric potential rate, also known as the Seebeck coefficient. The sign and magnitude of the Seebeck coefficient depend on the thermoelectric properties of the two conductors that make up the thermocouple and the temperature difference at the junction.
Currently, the International Electrotechnical Commission (IEC) recommends 8 types of thermocouples as standardized thermocouples, namely type T, type E, type J, type K, type N, type B, type R and type S.
2. Working principle of thermal resistance
The resistance value of the conductor changes with the temperature change, and the temperature of the measured object can be deduced by measuring its resistance value. The sensor constructed using this principle is a resistance temperature sensor. This kind of sensor is mainly used for temperature measurement in the temperature range of -200-500℃. Pure metal is the main manufacturing material of thermal resistors. The material of the thermal resistor should have the following characteristics: ① The temperature coefficient of resistance should be large and stable, and there should be a good linear relationship between the resistance value and temperature.
②High resistivity, small heat capacity and fast reaction speed.
③The material has good reproducibility and processability, and the price is low.
④The chemical and physical properties are stable within the temperature measurement range.
At present, platinum and copper are the most widely used in industry and have been made into standard temperature measuring thermal resistors.
3. Infrared temperature sensor
In nature, when the temperature of an object is higher than absolute zero, due to the existence of internal thermal motion, it will continuously radiate electromagnetic waves to the surroundings, including infrared rays with a wavelength range of 0.75 to 100 μm. Infrared temperature sensors are made using this principle.
SMTIR9901/02 is an infrared sensor produced by Smartec Company in the Netherlands and is widely used in the market. It is a silicon-based infrared sensor based on a thermopile. A large number of thermocouples are stacked on the underlying silicon base. The high-temperature and low-temperature contacts on the bottom layer are insulated from their heat by an extremely thin film. The black absorbing layer on the high-temperature contact converts incident radiation into heat energy. It can be known from the thermoelectric effect that the output voltage is proportional to the radiation. Usually thermopiles use BiSb and NiCr as thermocouples. In addition, SMT9902sil is embedded with a Ni1000 temperature sensor and a silicon filter with a small viewing angle, making the temperature measurement more accurate. Because infrared radiation characteristics are temperature dependent, different filters can be used to measure different temperature ranges. Mature semiconductor technology enables product miniaturization and low cost. To meet certain applications, the infrared sensor opening viewing angle can be designed as small as 7°.
4. Analog temperature sensor
Common analog temperature sensors include LM3911, LM335, LM45, AD22103 voltage output type, and AD590 current output type.
AD590 is a current output temperature sensor from Analog Devices. The power supply voltage range is 3~30V, the output current is 223μA (-50℃) ~ 423μA (+150℃), and the sensitivity is 1μA/℃. When the sampling resistor R is connected in series in the circuit, the voltage across R can be used as the output voltage. Note that the resistance value of R cannot be too large to ensure that the voltage at both ends of the AD590 is not less than 3V. The AD590 output current signal transmission distance can reach more than 1km. As a high-resistance current source, up to 20MΩ, it does not have to account for errors caused by additional resistance introduced by selector switches or CMOS multiplexers. Suitable for multi-point temperature measurement and remote temperature measurement control.
5. Logic output temperature sensor
Set a temperature range. Once the temperature exceeds the specified range, an alarm signal will be sent to start or shut down the fan, air conditioner, heater or other control equipment. At this time, a logic output temperature sensor can be used. LM56, MAX6501-MAX6504, and MAX6509/6510 are typical representatives.
LM56 is a high-precision low-voltage temperature switch produced by NS Company, with a built-in 1.25V reference voltage output. It can only carry a maximum load of 50μA. The power supply voltage ranges from 2.7~10V, the maximum operating current is 230μA, the sensitivity of the built-in sensor is 6.2mV/℃, and the sensor output voltage is 6.2mV/℃&TImes; T+395mV.
6. Digital temperature sensor
It uses a digital temperature sensor produced by silicon technology and uses a PTAT structure. This semiconductor structure has precise, good temperature-dependent output characteristics. The output of the PTAT is modulated into a digital signal through a duty cycle comparator. The relationship between duty cycle and temperature is as follows: DC=0.32+0.0047*t, t is degrees Celsius. The output digital signal is compatible with the microprocessor MCU. Through the high-frequency sampling of the processor, the duty cycle of the output voltage square wave signal can be calculated, and the temperature can be obtained. Due to its special process, this temperature sensor has a resolution better than 0.005K. The measuring temperature range is -45 to 130℃, so it is widely used in high-precision occasions.
Reasons and solutions for the rupture of the temperature sensor probe shell and sleeve
In many engineering applications, we found that the shell and casing of the temperature sensor probe in use will crack, which will affect the safety of the production machine operation, and in serious cases, accidents will occur. By investigating the rupture of the sensor probe shell and looking for the reasons, we found that the main reasons for the rupture of the temperature sensor sleeve are as follows:
(1) The temperature sensor probe is impacted by high-speed fluid, the load is too large, and the stress exceeds the limit, causing the probe to rupture;
(2) The processing defects of the temperature sensor probe itself lead to stress concentration and easily cause the probe to break;
(3) The pipeline vibrates too much, causing fatigue damage to the temperature sensor probe;
(4) When the fluid flows through the temperature sensor probe, it induces vibration of the temperature sensor probe. That is, the natural frequency of the temperature sensor probe resonates with the fluid vortex shedding frequency. This resonance phenomenon will cause the temperature sensor probe to be damaged more quickly and even break.
Based on the above situations that can easily lead to temperature sensor probe rupture, we conducted research together with thermal control majors and metal majors and found that the occurrence of temperature sensor probe rupture can be reduced through the following methods.
(1) Strictly control the insertion depth of the sensor probe. As the insertion depth increases, the force on the protective probe increases squarely. Therefore, when we measure temperature, we only need to insert the temperature sensor probe into the isothermal zone of the fluid without inserting it into the center point of the pipe. This will help shorten the length of the cantilever of the thermometer bag and reduce the amplitude of its endpoint.
(2) Optimize the diameter of the temperature sensor probe while ensuring the necessary sensor probe strength. Because when the diameter of the temperature sensor probe increases, the force on the watch bag increases linearly. Therefore, when selecting the diameter of the watch bag, it is necessary to reasonably ensure the strength of the probe and stagger the resonance danger zone as much as possible.
(3) Change the cross-sectional shape and process its surface into a structural form so that the fluid does not produce vortex shedding.
(4) Strictly control the quality of maintenance, conduct a good inspection of the material of the sensor probe, and also conduct a flaw detection inspection to strictly prevent the occurrence of abnormal accidents such as cracks and breaks in the welding joints.
(5) When the system is put into operation, avoid sudden full opening of the valves on the pipeline. When the valve is first put into operation and the valve is opened, the temperature sensor probe will bear a large one-way force. Therefore, when the system is first put into operation, the valve should be opened slowly to allow the system pressure to gradually rise and to minimize the pressure difference between the front and back of the temperature sensor casing. Prevent the probe from breaking due to excessive one-way force on the casing.
When any sensor is put into use, some unexpected situations will always occur. We must combine theory with practice and propose corresponding solutions to specific situations that occur.
How the temperature sensor works
There are four main types of temperature sensors: thermocouples, thermistors, resistance temperature detectors (RTDs), and IC temperature sensors. IC temperature sensors include two types: analog output and digital output.
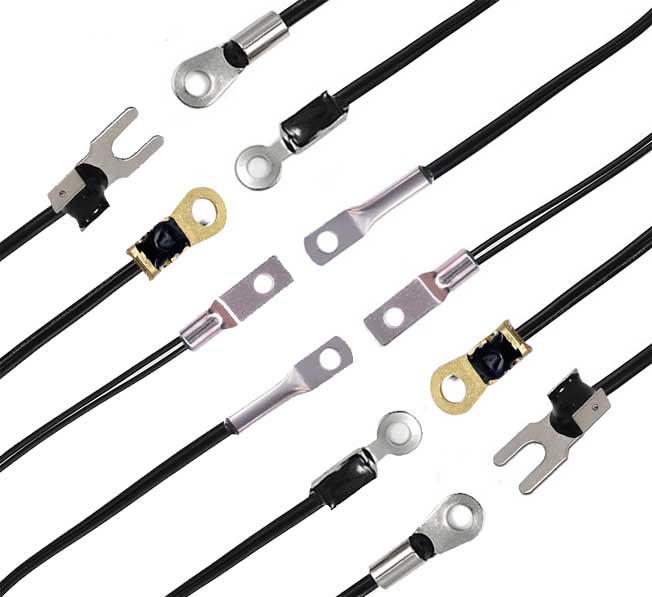
1. Working principle of thermocouple
When there are two different conductors and semiconductors A and B forming a loop, and the two ends are connected to each other, as long as the temperatures at the two nodes are different, the temperature at one end is T, which is called the working end or hot end. The temperature of the other end is TO, which is called the free end (also called the reference end) or the cold end. Then there will be current in the loop, that is, the electromotive force existing in the loop is called thermal electromotive force. This phenomenon of electromotive force generated due to temperature differences is called the Seebeck effect. There are two effects related to Seebeck: First, when a current flows through the connection of two different conductors, heat is absorbed or released (depending on the direction of the current), which is called the Peltier effect. Second, when a current flows through a conductor with a temperature gradient, the conductor absorbs or releases heat (depending on the direction of the current relative to the temperature gradient), which is called the Thomson effect. A combination of two different conductors or semiconductors is called a thermocouple. The thermoelectric potential EAB (T, T0) of the thermocouple is synthesized from the contact potential and the temperature difference potential. Contact potential refers to the potential generated at the contact between two different conductors or semiconductors. This potential is related to the properties of the two conductors or semiconductors and the temperature at the point of contact.
Thermoelectric potential refers to the potential generated by the same conductor or semiconductor at two ends with different temperatures. This potential is only related to the properties of the conductor or semiconductor and the temperature at both ends, but has nothing to do with the length, cross-sectional size of the conductor, or the temperature distribution along its length. Both contact potential and thermoelectric potential are potentials generated due to the difference in the number of electrons concentrated at the end points of the contact. The thermoelectric potential measured by a thermocouple is the composite of the two. When the loop is disconnected, there is an electromotive force difference ΔV between the disconnection points a and b, and its polarity and size are consistent with the thermoelectric potential in the loop. And it is stipulated that at the cold end, when the current flows from A to B, A is called the positive electrode and B is the negative electrode. Experiments show that when △V is very small, △V is directly proportional to △T. The differential thermoelectric potential of △V versus △T is defined as the thermoelectric potential rate, also known as the Seebeck coefficient. The sign and magnitude of the Seebeck coefficient depend on the thermoelectric properties of the two conductors that make up the thermocouple and the temperature difference at the junction.
Currently, the International Electrotechnical Commission (IEC) recommends 8 types of thermocouples as standardized thermocouples, namely type T, type E, type J, type K, type N, type B, type R and type S.
2. Working principle of thermal resistance
The resistance value of the conductor changes with the temperature change, and the temperature of the measured object can be deduced by measuring its resistance value. The sensor constructed using this principle is a resistance temperature sensor. This kind of sensor is mainly used for temperature measurement in the temperature range of -200-500℃. Pure metal is the main manufacturing material of thermal resistors. The material of the thermal resistor should have the following characteristics: ① The temperature coefficient of resistance should be large and stable, and there should be a good linear relationship between the resistance value and temperature.
②High resistivity, small heat capacity and fast reaction speed.
③The material has good reproducibility and processability, and the price is low.
④The chemical and physical properties are stable within the temperature measurement range.
At present, platinum and copper are the most widely used in industry and have been made into standard temperature measuring thermal resistors.
3. Infrared temperature sensor
In nature, when the temperature of an object is higher than absolute zero, due to the existence of internal thermal motion, it will continuously radiate electromagnetic waves to the surroundings, including infrared rays with a wavelength range of 0.75 to 100 μm. Infrared temperature sensors are made using this principle.
SMTIR9901/02 is an infrared sensor produced by Smartec Company in the Netherlands and is widely used in the market. It is a silicon-based infrared sensor based on a thermopile. A large number of thermocouples are stacked on the underlying silicon base. The high-temperature and low-temperature contacts on the bottom layer are insulated from their heat by an extremely thin film. The black absorbing layer on the high-temperature contact converts incident radiation into heat energy. It can be known from the thermoelectric effect that the output voltage is proportional to the radiation. Usually thermopiles use BiSb and NiCr as thermocouples. In addition, SMT9902sil is embedded with a Ni1000 temperature sensor and a silicon filter with a small viewing angle, making the temperature measurement more accurate. Because infrared radiation characteristics are temperature dependent, different filters can be used to measure different temperature ranges. Mature semiconductor technology enables product miniaturization and low cost. To meet certain applications, the infrared sensor opening viewing angle can be designed as small as 7°.
4. Analog temperature sensor
Common analog temperature sensors include LM3911, LM335, LM45, AD22103 voltage output type, and AD590 current output type.
AD590 is a current output temperature sensor from Analog Devices. The power supply voltage range is 3~30V, the output current is 223μA (-50℃) ~ 423μA (+150℃), and the sensitivity is 1μA/℃. When the sampling resistor R is connected in series in the circuit, the voltage across R can be used as the output voltage. Note that the resistance value of R cannot be too large to ensure that the voltage at both ends of the AD590 is not less than 3V. The AD590 output current signal transmission distance can reach more than 1km. As a high-resistance current source, up to 20MΩ, it does not have to account for errors caused by additional resistance introduced by selector switches or CMOS multiplexers. Suitable for multi-point temperature measurement and remote temperature measurement control.
5. Logic output temperature sensor
Set a temperature range. Once the temperature exceeds the specified range, an alarm signal will be sent to start or shut down the fan, air conditioner, heater or other control equipment. At this time, a logic output temperature sensor can be used. LM56, MAX6501-MAX6504, and MAX6509/6510 are typical representatives.
LM56 is a high-precision low-voltage temperature switch produced by NS Company, with a built-in 1.25V reference voltage output. It can only carry a maximum load of 50μA. The power supply voltage ranges from 2.7~10V, the maximum operating current is 230μA, the sensitivity of the built-in sensor is 6.2mV/℃, and the sensor output voltage is 6.2mV/℃&TImes; T+395mV.
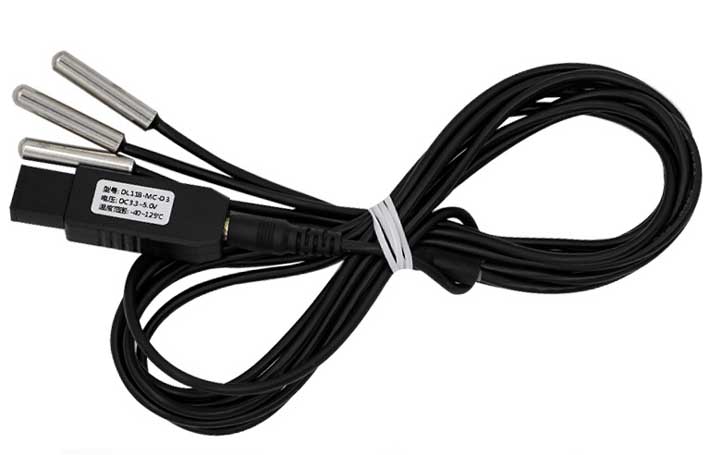
It uses a digital temperature sensor produced by silicon technology and uses a PTAT structure. This semiconductor structure has precise, good temperature-dependent output characteristics. The output of the PTAT is modulated into a digital signal through a duty cycle comparator. The relationship between duty cycle and temperature is as follows: DC=0.32+0.0047*t, t is degrees Celsius. The output digital signal is compatible with the microprocessor MCU. Through the high-frequency sampling of the processor, the duty cycle of the output voltage square wave signal can be calculated, and the temperature can be obtained. Due to its special process, this temperature sensor has a resolution better than 0.005K. The measuring temperature range is -45 to 130℃, so it is widely used in high-precision occasions.
Reasons and solutions for the rupture of the temperature sensor probe shell and sleeve
In many engineering applications, we found that the shell and casing of the temperature sensor probe in use will crack, which will affect the safety of the production machine operation, and in serious cases, accidents will occur. By investigating the rupture of the sensor probe shell and looking for the reasons, we found that the main reasons for the rupture of the temperature sensor sleeve are as follows:
(1) The temperature sensor probe is impacted by high-speed fluid, the load is too large, and the stress exceeds the limit, causing the probe to rupture;
(2) The processing defects of the temperature sensor probe itself lead to stress concentration and easily cause the probe to break;
(3) The pipeline vibrates too much, causing fatigue damage to the temperature sensor probe;
(4) When the fluid flows through the temperature sensor probe, it induces vibration of the temperature sensor probe. That is, the natural frequency of the temperature sensor probe resonates with the fluid vortex shedding frequency. This resonance phenomenon will cause the temperature sensor probe to be damaged more quickly and even break.
Based on the above situations that can easily lead to temperature sensor probe rupture, we conducted research together with thermal control majors and metal majors and found that the occurrence of temperature sensor probe rupture can be reduced through the following methods.
(1) Strictly control the insertion depth of the sensor probe. As the insertion depth increases, the force on the protective probe increases squarely. Therefore, when we measure temperature, we only need to insert the temperature sensor probe into the isothermal zone of the fluid without inserting it into the center point of the pipe. This will help shorten the length of the cantilever of the thermometer bag and reduce the amplitude of its endpoint.
(2) Optimize the diameter of the temperature sensor probe while ensuring the necessary sensor probe strength. Because when the diameter of the temperature sensor probe increases, the force on the watch bag increases linearly. Therefore, when selecting the diameter of the watch bag, it is necessary to reasonably ensure the strength of the probe and stagger the resonance danger zone as much as possible.
(3) Change the cross-sectional shape and process its surface into a structural form so that the fluid does not produce vortex shedding.
(4) Strictly control the quality of maintenance, conduct a good inspection of the material of the sensor probe, and also conduct a flaw detection inspection to strictly prevent the occurrence of abnormal accidents such as cracks and breaks in the welding joints.
(5) When the system is put into operation, avoid sudden full opening of the valves on the pipeline. When the valve is first put into operation and the valve is opened, the temperature sensor probe will bear a large one-way force. Therefore, when the system is first put into operation, the valve should be opened slowly to allow the system pressure to gradually rise and to minimize the pressure difference between the front and back of the temperature sensor casing. Prevent the probe from breaking due to excessive one-way force on the casing.
When any sensor is put into use, some unexpected situations will always occur. We must combine theory with practice and propose corresponding solutions to specific situations that occur.